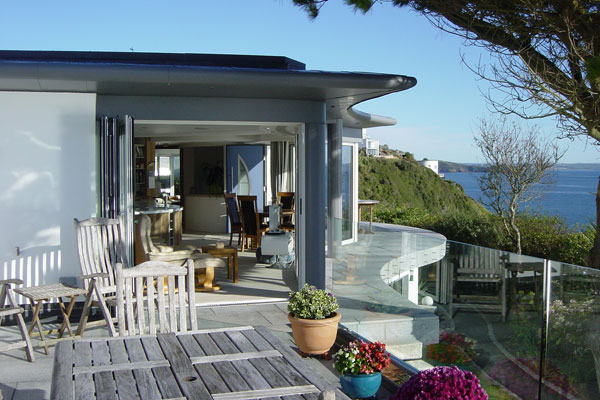
Sunfold installed 1 x 5 panel segmented, 1 x 3 panel, 1 x 2 panel, 1 x 6 panel curved fixed, 1 x 8 panel curved fixed. Top hung in RAL9002, grey white, fully weathered
The owners bought the plot then known as “Kerals” in 2003. On it was a tatty old mobile home, which they replaced with the biggest and latest in static caravans, to which they added a conservatory. It was used as a holiday home for several years and the ‘jungle’ which covered the plot, was cleared and new gardens were planted.
The unusual bonus of the plot, was that it has access to its own private beach (owned to low water mark), which is inaccessible to anyone other than via the sea.
Being a qualified architect, the owner was itching to see if he could get planning to build a permanent dwelling on the site and produced some ‘doodles’ for discussion with the planners.
It was always going to be a difficult task, as the site is in an Area of Outstanding Beauty, part of the Heritage Coast and outside the Development Envelope for Mevagissey.
Because there was a permanent use for a holiday caravan with year round occupation, the owner was able to argue that he could put a demountable building on the site – being up to 60 feet long, 20 feet wide and 10 feet floor to ceiling with any roof pitch and constructed of any materials – all without planning permission, as these are the provisions of the Caravan Act!
The other problem was the site’s proximity to the cliff and coast, where there is a presumption against building houses unless it can be demonstrated that the site has a life of at least 100 years. This involved the commissioning of geological engineering professionals to undertake a study, which concluded that, subject to various stabilising techniques, the most draconian of which involved the placing of 1300 tonnes of rock armour at the cliff base to arrest any further potential coastal erosion, then the site was appropriate for the construction of a new dwelling.
The planners were persuaded that a contemporary house of good design would be far preferable to the alternative and agreed to grant permission subject to the rock armour being in place before construction began ………..AND……….subject to the dwelling being restricted to holiday use only!!
The owners successfully appealed against the holiday occupancy condition, which was removed on appeal and then arranged for the Rock Armour to be brought and placed at the cliff base. This was a lengthy and expensive process (£100K) and was taking too long to complete. Without it being completed, construction could not commence – so they applied for an amendment to the planning condition and obtained permission to commence construction – so long as occupation did not take place until the cliff stabilisation works were complete.
Construction of The Wave House started in January 2011 with the shell and external works being completed by an excellent local contractor JJJones and Sons Limited, by Christmas 2011. The owners then set to and project managed the fit out of the interior, much of the Kitchen, Bathroom and Lounge fittings he did himself – being a bit of a handy lad as well as an architect! The project was completed they moved in at the end of April 2012.
Solar PV was installed to generate electricity just before the newly imposed Government 10 December 2011 deadline, to secure the 43p per Kw (around £1300 has been received for electricity generated during the first 12 months of operation).
The rest of the roof was covered with Sedum to soften its appearance to near neighbours who had supported his ideas.
An Air Source Heat Pump provides energy to drive the under-floor wet system of central heating and provide hot water. Cooking is through an off- peak storage heated AGA, supplemented by combination microwave and steamer units. So the house is all electric!
The design which the owner created himself, was dependant on large areas of glass facing the sea views and terraces and the curvilinear style was what he wanted to achieve as part of his design ethos -based on the waves of the sea.
Several suppliers of folding sliding doors and screens were considered – not many – in fact only two – being able to supply curved folding sliding doors. Originally the owner wanted all 5 sets of screens to be folding sliding, but costs were prohibitively high and so it was resolved to have only 3 of the 5 sets that could be opened, (in this country’s climate, there are few days in the year which would be conducive in any event).
The owner had used Sunfold Systems on other projects and was impressed with the detailing and engineering and so decided to place the contract with Sunfold fo the supply and installation. Due to the steel contract not due to be complete for 20 weeks, the owner decided to provide Sunfold with CAD information and fully dimensioned steelwork drawings with the several differing radii. The result……………..everything fitted perfectly to within the 5mm tolerances allowed for Sunfold’s installation, which according to the owner ‘was carried out with utmost professionalism and attention to detail’.
Since the installation the owners have been absolutely delighted with the product and Sunfold’s after sales service …………which is second to NONE!! In their words ‘A brilliant product – by a brilliant company’.